Horsepower, horsepower and more horsepower! This was the cry of big acreage American and Canadian farmers of the middle 1970s. Rising fuel prices, increased costs for seed and fertilizer, falling commodity prices and the mass exodus of rural families— who had supplied low cost farm labor to urban and suburban areas to find higher paying jobs with regular hours and benefits in the increasingly difficult economic conditions—led to the need for farmers to be able to operate more acres with less expense and labor.
Bigger crop production with less manpower meant one man needing to do the work that two or more had previously done. Larger tools covering more acres per day were the answer, requiring tractors of more size and power as well as operator comfort. Since 1967, Massey had been a leader in the industry, supplying some of the highest horsepower tractors on the market starting with the 136 horsepower 1150 and later in 1973 with the 141 horsepower 1155, both powered by big Perkins V8 diesel engines. Yet the demand for more horsepower, more transmission speeds and quieter and more comfortable cabs for nearly continuous day and night operation continued to rise.
While Massey had kept up very well in the horsepower race, it was decidedly behind the competition as far as transmissions and operator comfort were concerned. While the Massey 1155’s eight-speed transmission with Multi Power provided 16 speeds forward and four in reverse, both John Deere’s Quad-Range and IH’s Torque Amplifier transmissions utilized only two shift levers while Massey used three. As far as the operator’s comfort was concerned, Massey’s cabs were no match for the quietness and low vibration levels of either John Deere’s Sound Gard body or IH’s cab forward design on its 8 series tractors and Massey’s market share was hurting as a result.
A totally new approach was taken by Massey engineers to create new row crop tractors that addressed all these shortcomings. The first of the new 2000 series tractors appeared in 1976 as the 2800. Weighing in at more than 14,000 pounds and rated at 190 horsepower, this massive giant was the most powerful two-wheel drive tractor on the market, not to mention the heaviest.
Its nearest competition, horsepower wise, was the Allis-Chalmers 7080 at 181 PTO horsepower. John Deere’s 6030 was only 176 horsepower and IH’s 1586 was just 162 horsepower. But the really exciting news was that it finally seemed as though Massey had finally caught up with the competition in transmissions and operator comfort. The spring actuated, 14 inch dual dry disc ceremetalic clutch transmitted the engine power to either the standard eight speed transmission or the optional all new 24 speed transmission. The 24 speed transmission featured the same eight speed gearbox as the standard transmission, but sending the power to this new heavy duty drive train was a three speed on-the-go power shift input unit.
Creating 24 forward speed ratios and providing a forward/ reverse shuttle in the four lowest gears, the 2800 had more gears to choose from than any other farm tractor! The two shift levers were mounted to the right of the operator on a control column that was easily within the operator’s reach. The lower lever selected one of the eight main gear ratios while the upper lever not only controlled the three power shift range, but also served as the forward/reverse shuttle control. This arrangement allowed the operator to choose the best average gear for the job being done with the power shift in the intermediate range and then shift into high or low range for changing field conditions.
As exciting as the new 24 speed transmission was to Massey and its customers, possibly even more important news was the completely new “comfort and convenience engineered” cab. With this cab, comfort and convenience indeed reached a whole new level. The first of Massey’s tractors to boast over 7,000 square inches of tinted glass (7,336 to be exact) featured a onepiece windshield with glass extending down to the cab floor along each side of the engine cowl. Operator visibility was second to none with this cab. The roomy, extra quiet cab interior featured a luxury six way, adjustable seat with folding armrests, as well as a tilting and telescoping steering wheel for the hydrostatic power steering. All cab controls were designed and located for minimum operator effort and maximum comfort and efficiency for long days and nights in the field.
The hydraulic control levers for the lower link draft sensing three-point hitch and the standard two spool or optional three spool auxiliary remotes were located next to the operator’s right and just behind the transmission shift levers, providing almost effortless control of all these functions. In the best tradition of the Ferguson system, the three-point hitch incorporated position and draft modes of operation, with infinitely variable draft intermix sensitivity using feedback from the lower links. Twin externally mounted 2-7/8 inch diameter cylinders provided the lifting power. The extra long throttle lever was mounted to the right of the instrument panel cowl within easy reach of the operator without leaning forward. It featured a cross piece handle instead of a knob for more comfortable operation. The tachometer, fuel level gauge and coolant temperature gauge were mounted on the new anti-glare wood grain instrument panel, as was a panel of 12 warning lights, allowing the operator to monitor every vital tractor function at a glance.
Powering this huge machine was a 640 cubic inch Perkins V8 diesel engine, of course, the largest engine in any two wheel drive tractor of any make. This engine was turbocharged and featured dual engine oil filters. A CAV model DP15 rotary high pressure fuel injection pump was used, designed to reduce fuel and maintenance costs. Dry replaceable cylinder sleeves, cross bolted main bearing caps and a forged crankshaft with bolt on counterweights were just some of the heavy duty features of this engine. A bore and stroke of 4.63 by 4.75 inches with a compression ratio of 15:1 produced rated horsepower at 2,500 RPM.
The open center hydraulic system featured three separate pumps. The transmission-driven main pump was a dual gear type with a high pressure circuit for the three-point hitch and the optional third auxiliary remote valve with an output of 16.5 GPM and a low pressure circuit for brake cooling, the PTO clutch, the 24 speed transmission clutch packs and the differential lock, with an output of 6.4 GPM. The 16.5 GPM auxiliary gear pump was also transmission driven and provided hydraulic power to the two standard auxiliary remote valves. An engine driven pump with a 5.5 GPM output provided power for the hydrostatic steering. Combined, the total capacity of these three pumps was a whopping 38.5 GPM!
The braking system featured 16 1/4. inch diameter single disc power assisted wet brakes on each rear axle. The parking brake handle operated a shoe on the outside of the rear axle ring gear. A hydraulically operated differential lock was available as optional equipment.
Such a large tractor required suitably large fluid capacities. The rear mounted fuel tank located behind the cab held 87 gallons of diesel fuel. The cooling system held nearly 14 gallons of coolant, the engine crankcase held six gallons of oil and the transmission and hydraulic system required 38 gallons of PermaTran III hydraulic/ transmission fluid.
In 1978, the 2800 was replaced with the 2805. This year also saw the introduction of the rest of the 2000 series family—the 2675 with 100 horsepower, the 2705 with 120 horsepower, the 2745 with 140 horsepower and the 2775 with 160 horsepower.
All these tractors shared most of the same features as the 2805 with the exception of the engine equipment. The 2675 and 2705 were powered by two different versions of the Perkins 354 C ID six cylinder diesel engine, with the 2675 using a naturally aspirated version and the 2705 being equipped with a turbocharger. The 2745, like the 2775 and the2805, was powered by a Perkins V8. lts 540 cubic inches were naturally aspirated, as was the 640 CID engine in the 2775. The 2805, like the 2800, was equipped with the turbocharged version of the 640 CID engine.
The high hopes held by Massey for these revolutionary tractors began to fade rather quickly due to what turned into a long series of unfortunate problems, some caused by inadequate engineering and others caused by other factors. Many of these involved the new 24 speed transmission that had held so much promise in Massey’s battle with the other mainline tractor manufacturers. The basic eight speed transmission was reliable and trouble free for the most part, but the 24 speed version was a completely different story.
The 24 speed power shift input unit consisted of three main clutch elements: low, intermediate and high. The low and high clutches were hydraulically engaged, while the intermediate clutch was engaged by spring pressure and disengaged hydraulically. In low range, the low clutch pack was pressurized to engage it, while hydraulic pressure disengaged the intermediate clutch. The same principle was used in high range, with the high pack being pressurized for engagement and the intermediate pack again being hydraulically disengaged. In intermediate range, all packs were de-pressurized, with the intermediate then being engaged by spring pressure. Anything that prevented these clutches from being pressurized at the proper time, sequence and pressure could cause a catastrophic failure due to two clutches trying to engage at the same time. When deaIing with this kind of horsepower, catastrophic failure could literally happen in seconds.
When I was working as a technician for the local Massey dealer between 1983 and 1986, I remember at least two of these units that I had removed from the tractor, opened up and just dumped out the chunks of metal and clutch discs. The entire units had been reduced to basically nothing but scrap! In fact, Massey service information covering the troubleshooting and repair of these units stated several times that if improper pressures were found in the three clutch circuits during initial testing and the tractor had been operated for any length of time this way, it was recommended the complete three speed input section be replaced and repair not even be attempted! It was easy to see why.
Symptoms that indicated such damage were numerous: loss of reverse, which was only driven in low, indicating a low clutch pack failure; stalling or laboring of the engine when shifting between ranges; drive in intermediate range only or complete loss of intermediate range; loss of high range; noise when shifting between ranges. The actual causes of these problems were even more numerous and difficult to discover for dealers when failures first started showing up: control valve gaskets blown between passages, low pressure due to incorrectly operating pressure regulating valves, a-ring and piston seals blown out due to faulty regulating valves causing pressures to be too high, low supply pump volume, incorrect control valve linkage adjustment or control valve spool ticking in their bores, just to name a few.
To try to reduce the possible failures when using high or low range, Massey issued a service bulletin to their dealers stressing the importance of properly training operators of the tractors with 24 speed transmissions to run in intermediate range as much as possible and to use the high and low range only with light loads. Farmers didn’t like the idea of not being able to fully use the speed to-work tailoring capabilities that this transmission had supposedly offered and had been a major reason that many had purchased them in the first place! To add to the seriousness of the situation, several parts, such a input shaft gears, seals, bearings, screws and even the rear covers on some of the failed units were found to be defective or not manufactured to the correct specifications. Most of these components had been manufactured for Massey by outside suppliers.
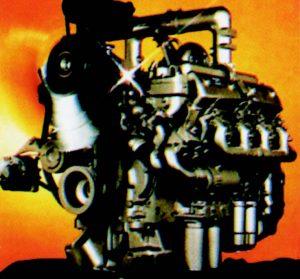
Other more sinister factors were found when some of these failed units were disassembled and inspected— missing and incorrectly installed parts!
Labor/ management relations at Massey’s Detroit, Michigan assembly plant where these tractors were built were severely strained during the late ‘70s and early ‘80s and it was rumored that disgruntled employees were deliberately “sabotaging” tractors during assembly, further adding to the headaches of Massey, its dealers and most importantly, the customers, who were beginning to think it was definitely their misfortune to own one of these tractors.
The 24 speed transmission wasn’t the only problem. Oil leakage at the clutch input shaft seal was caused by the seal being cut during factory assembly due to a sharp edge on the shaft. Grinding a radius on the shaft to remove the sharp edge was the first solution, followed by an updated seal, followed by a recommendation of installing the seal in reverse to further help prevent seal lip damage by the shaft during re-assembly. Excessive back pressure in the power steering return oil circuit of the VS powered machines, which was connected to the brake cylinder return line, could cause partial engagement of the brakes during operation.
The first recommendation was to service the filter more often. When this had little effect, a bulletin was issued to recommend removing the filter entirely. When that didn’t work, the separate power steering pump was eliminated altogether, with the steering now being powered through a priority valve on the high pressure side of the main hydraulic pump as the 2675 and 2705 had been since the start of production. The stated reasons for this change were to provide improved steering at low RPMs and to eliminate congestion in and around the vee of the engine. This change was made in production of the 2745, 2775 and 2805s at serial number 9R7585. At serial number 9R7813, the park lock on all tractors was changed from a brake on the differential to a gear engaging pawl. Th original brake was simply not adequate for tractors of this size, especially if implements were hitched to them. A park lock modification kit was then made available for installation on previous production tractors, which were installed by dealers at no cost to the owner.
The engine fuel system was also a source of difficulties on the VS models. The CAY model DP15 rotary injection pump was prone to leaking and seizing. To make matters worse, only a handful of diesel fuel system repair facilities in the U.S. and Canada were authorized to even repair them, let alone repair them under CAV warranty. In June of 1980, it was announced that the troublesome pump was being replaced in production with a Robert Bosch model MW in-line pump. Also cut into production at this time were two spin-on fuel filters to replace the two CAV cartridge type filters used previously. The electric engine shut-off used on the DPl5 was also eliminated and replaced by a less problematic second detent on the throttle lever, with the engine shutting off when the lever was pushed past the idle detent. (Incidentally, this makes it easy to determine which pump is on the tractor without even looking at the pump.) Later in 1980, a program was released by Massey for certain previous production V8 tractors to replace the injection pump, engine cylinder heads (due to low service life of intake and exhaust valves) and to modify the steering system. In addition, Massey was extending the warranty on the affected machines an additional 12 months from the date of the modifications or 24 months from the original purchase date, whichever provided the longest coverage.
Other issues had to be addressed in the tumultuous first years of production, dealing with inadequate three-point hitch lifting ability of the V8 powered tractors requiring increasing the lift cylinder bores from 2-7/8 inches to 3-1/8 inches, raising the lift capacity from 8,030 pounds to 9,400 pounds. This was due, no doubt, to ingenious farmers attaching the largest implements they could to take advantage of the huge load pulling capacity of these tractors. This change was cut into production at serial number 9R6655. PTO clutch and brake slippage had become apparent as well, a problem that was solved by redesigning the brake return spring, clutch discs and clutch pack piston.
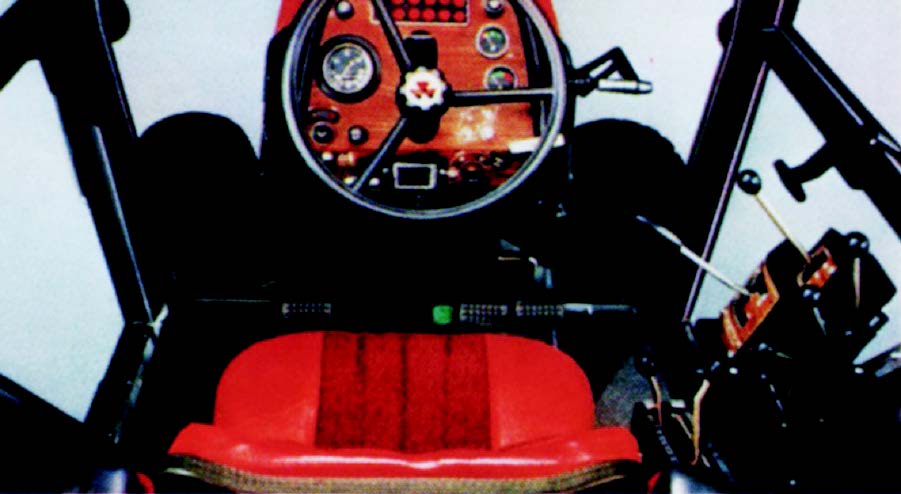
By about 1982, most of the bugs had been worked out, with exception of the 24 speed transmission. Even after all the defective parts and assembly issues had been addressed, it was still apparent that this transmission would continue to be a problem, as failures still continued to occur. The lack of adequate interlock protection between the clutch circuits continued to allow more than one clutch pack to become engaged at the same time under certain conditions. Many frustrated customers, figuring they were stuck with a lemon and just had to make the best of a bad situation, had their headaches somewhat alleviated by getting rid of the three speed power shift input unit entirely and converting to the plain eight speed transmission. It is safe to say that many loyal customers had their belief in MF quality destroyed by these tractors.
In addition, all the warranty repairs and modifications done by the company to try to salvage their reputation had cost enormous sums of money. Dealers also took big hits, not only incurring un-reimbursed expense to haul the “dead” tractors out of the farmer’s field during the busy seasons and in many cases providing loaner tractors to get their field work done, but as anyone who has ever had anything to do with warranty work at a farm equipment dealership can tell you, there is sometimes a lot of labor involved in just trying to diagnose the problem, which in many cases is not reimbursed to the dealer. Farmers comparing notes on their bad experiences led them to conclude that Massey was now building “junk,” costing the dealers huge numbers of lost sales, probably leading to the demise of more than a few who had just been hanging on by a thread in the down economic conditions of the times as it was. As far as Massey was concerned, the failure of the 2000 series had helped them dig themselves an even bigger financial hole than they had already been in, ultimately leading to the closing of the Detroit plant in 1982. It was a very sad time for Massey Ferguson, its dealer and its previously loyal customers.
Production of the 2000 series
ended with the closing of the Detroit plant in 1982. Only 13,525 total units of all models had been built. Compare this to 55,346 John Deere 4440s alone produced between 1978 and 1982! The tractors that had been the great hope for the future of Massey in North America had turned into one of its biggest disasters. But, as we now know, Massey made a valiant effort to bounce back with the French built 2640 and the later 3000 series tractors. Massey couIdn’t be counted out just yet!
In recent years, there has been a resurgence of interest in the 2000 series Masseys, some out of nostalgia, some out of the need for cheap horsepower. If you are looking at buying one of them, the later the serial number, the better. If you are looking at one with a 24 speed transmission that has all the gears operating, be sure to do a thorough test drive, shifting through all the gears and ranges while applying the brakes at times to load the transmission. No slippage or loud noises should be evident. If they are, it might be best to walk away. Parts that are still available for these transmissions are very expensive and you would probably need to plan on spending at least into the thousands to repair it. If it is operating okay and you decide to go for it, use the transmission as Massey advised—intermediate range most of the time, especially under heavy load. The thing about these tractors is that they are just AWESOME to look at and especially to drive. Even I would have trouble walking away from one!